在制造业数字化转型的实践中,宁波优德普通过ERP(企业资源计划)与MES(制造执行系统)的深度对接,构建了一套贴合实际需求的生产进度实时监控方案。该方案以数据互通为核心,覆盖从计划层到执行层的全流程管理,帮助企业实现生产透明化与效率提升。
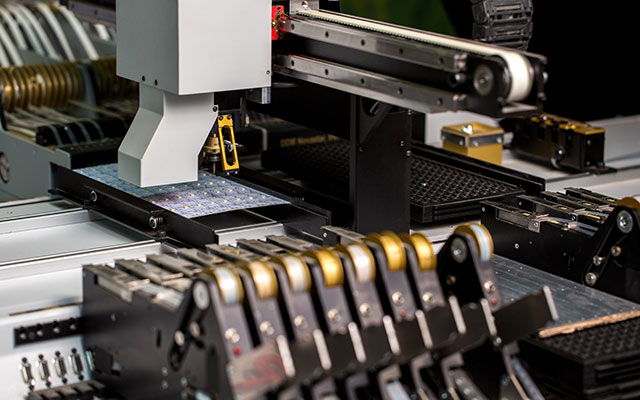
一、方案背景:从数据隔离到全流程协同
传统制造企业常面临ERP系统与车间执行层的信息断层问题:ERP制定的生产计划难以实时适配设备状态、物料供应等动态因素,导致计划与实际执行脱节。宁波优德普的解决方案通过打通ERP与MES的数据壁垒,将订单计划、资源调度、设备运行等环节串联,形成“计划-执行-反馈”的闭环管理。
例如,某汽车零部件企业曾因设备故障导致订单延误,ERP系统无法感知车间异常,而MES的实时监控功能可即时捕捉设备停机信号,并动态调整排产计划,避免连锁反应。
二、核心功能模块解析
1. 生产计划动态适配模块
·功能设计:将ERP下发的订单计划拆解为车间可执行的工序任务,结合设备状态、物料库存、人员排班等实时数据,自动生成动态排程。
·实际应用:当某生产线因故障停机时,系统自动将任务分配至空闲设备,并通过看板推送调整后的工序指令至操作终端,减少人工干预。
2. 全链路数据采集与监控模块
·硬件支持:通过IoT传感器、RFID标签等设备,实时采集设备运行参数(如温度、转速)、物料消耗量、工艺达标率等数据。
·可视化看板:车间大屏与移动端同步显示生产进度、异常报警(如设备超负荷、质量偏差),支持按订单、工段、班组等多维度穿透查询。
3. 质量追溯与闭环管理模块
·批次管理:从原材料入库到成品出库,每个环节绑定标识码,扫码即可追溯供应商批次、加工参数、质检记录。
·异常处理:当检测到不良品时,系统自动冻结同批次产品,并触发根因分析流程,缩短问题响应时间至10分钟内。
4. 资源调度优化模块
·物料协同:根据生产进度预测物料需求,自动触发采购申请或仓库调拨指令,避免产线待料。
·设备维护:基于设备运行数据预测故障周期,生成预防性维护计划,减少非计划停机时间。
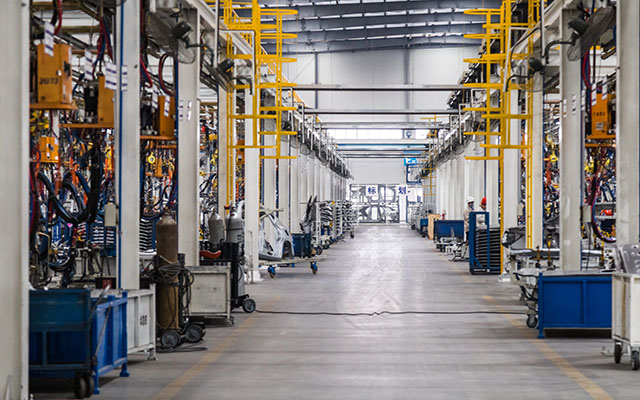
三、系统对接的关键技术实现
1. 数据接口标准化
·采用OPC UA协议实现ERP与MES的实时通信,确保订单信息、工艺参数、库存状态等字段的无缝传输。
·支持与主流ERP系统(如SAP、用友)的预配置对接模板,降低企业集成成本。
2. 边缘计算与云端协同
·在车间部署边缘服务器,对高频采集的传感器数据进行本地预处理(如异常过滤、聚合计算),再上传至云端分析平台,减少网络负载。
3. 权限分级与安全保障
·按角色划分数据访问权限(如操作工仅查看工序指令,管理层可调阅全厂报表),并通过区块链技术对关键工艺参数进行防篡改存证。
四、落地价值与客户反馈
宁波某家电制造企业引入该方案后,生产计划调整效率提升40%,物料错配率下降65%,客户投诉率减少32%。其生产主管反馈:“过去依赖经验判断设备负荷,现在系统能直接给出优化建议,车间调度更科学。”
五、未来升级方向
宁波优德普计划进一步融合数字孪生技术,通过3D建模还原车间实景,实现虚拟调试与物理生产的双向交互。同时,开发轻量化配置工具,支持企业自主调整监控指标与报警阈值。
通过ERP与MES的深度协同,宁波优德普的方案为制造企业提供了从“计划可靠”到“执行可控”的完整路径,成为区域制造业数字化转型的典型实践。
关于宁波优德普>>>
了解更多SAP ERP管理系统成功案例>>>
或拨打宁波优德普免费咨询热线:400-8045-500